Sandesh Gases Private Limited
Sandesh Gases Pvt Ltd. is a Group of SIG Company, poised to create new milestones. The SIG Group has a proven track record of over three decades and are leaders in Industrial, Medical Gases and associated products since last 40 years.
SANDESH GASES PVT LTD was founded in 2012 by a group of SANDESH INDUSTRIAL GASES ( SIG GROUP ) to meet the rising demand for Industrial gases, Cryogenic Bulk Liquid supply, Calibration Gas Mixtures And High purity Gases in the national & international markets. We believe in supplying quality products meeting international standards. We are also business partners of our customers to understand and meet their requirements and exceed their expectation to improve productivity and product quality. We are continuously improving in the field of “Traceability of Gas Mixtures”. Such Mixtures prepared as per customer’s specific requirement are used for calibration of analytical / diagnostics instruments, process analyzers ,online gas chromatography and in industrial process. We provide Traceable Gas Mixtures to various industries, E.g. Oil and Gas, Automotive and many others, as per customer requirement. We use devices and reference material which are traceable to international meteorological institutes. E.g. NABL.. All our customers are delighted and benefited by using our International Quality Gas Mixtures by saving valuable foreign exchange, inventory and time.
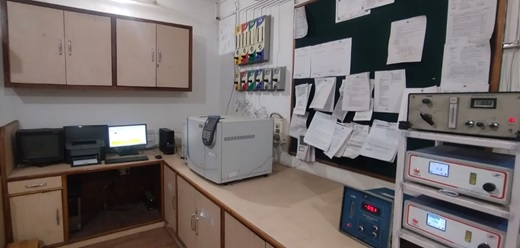
Analytical Services
Our Laboratory is equipped with high resolution instruments like gas Chromatographs and other analysers, with wide range of detectors and chromatographic columns to facilitate quantification and certification of components with least uncertainties. The carrier gases used for insrrtuments are of highest purity We can do testing and certification of gas samples at our laboratory by using our gas standards. We can also do revalidation of supplied gas mixtures whose stability period is getting expired.
Gas system Designing for laboratory
In almost any laboratory or research and scientific facility, there are numerous devices, instruments, or processes that require gases to run the instrumentation or process or to calibrate the devices. Gas cylinders that are located in the laboratory area can present significant hazards, and the space they take up can be better used for other more appropriate purposes. Gas delivery systems that are properly designed, sized, and located can improve safety in the laboratory. In addition, attention to high-purity requirements—purity, compatibility, flow, materials of construction, and more—is vital for safety, performance, and cost-efficiency. There are a number of codes and standards that apply to the storage, use, and installation of gases and their delivery systems
Gas Requirement Audit
The first step in properly designing any gas installation, whether it is for a new facility or a retrofit, is to conduct an audit or survey of the gases required for each location or laboratory. Identifying what gases are required for each instrument, their purity level, required delivery pressure, and peak flow demand is essential in determining everything from the size of the piping required, to the storage area required, and even the mode or source in which the gas may be supplied. Overestimating the pressure or flow requirements can result in higher installation costs and reduced gas savings resulting from residual contents left in cylinders or higher monthly rental fees on cylinders that are not required. Underestimating, however, can cause inefficient supply of gas to critical instruments or systems that impair their use or operation.
Selecting a Location for Storage and Gas Delivery Systems
There are some very specific storage and separation requirements for the areas in which compressed or cryogenic gases are stored and/or connected to a building’s gas delivery system. As a minimum, gas cylinders should be stored and secured in an upright position using brackets, chains, or straps in a well-lit and ventilated area away from combustible materials and sources of heat or ignition.
Pipe Sizing and Flow Considerations
When determining what size pipe or tubing to use for a specific application, the main consideration is to determine what the maximum required flow for that specific gas would be if all application or use points were flowing to their maximum at the same time. This can be found by totalling the individual use points and applying a conservative safety factor to allow for growth of requirements of at least 20–50%, depending on what the future outlook is for that gas
Choosing the Right Gas Delivery System
For almost all laboratory gases, maintaining gas purity is a critical requirement. To that end, the choice of materials of construction and their compatibility with that specific gas and its purity level must be considered. It is not enough that the materials are compatible with the specific gas, but that the design ensures and retains the purity of the gas. From the inlet to the outlet, a system that is designed with either bar stock brass or 316L stainless steel components is desired over forged components. Any diaphragms should be made of 316L stainless steel, and the diaphragm seals should be of a metal-to-metal design. Though there are many other areas that must be considered, the primary areas of concern are where to locate the gas storage area outside the laboratory, how much gas will be required, and how the gas will be delivered to the end use points. Users who follow these guidelines are well on their way to selecting a safe and cost-effective gas delivery system.
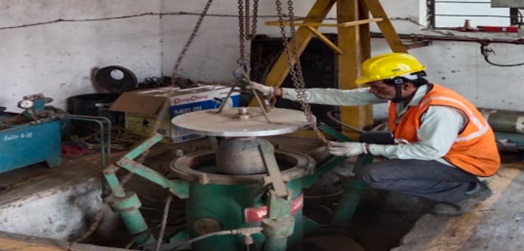
Cylinder Hydro Testing Shop
What is cylinder hydrotesting?
Hydrostatic Testing is a nondestructive test procedure used to check cylinders for leaks, structural flaws, durability, and corrosion. It is used to check a cylinder’s structural integrity. Testing consists of enclosing a cylinder filled with water inside a test jacket filled with water. Pressure is then applied internally to the cylinder, causing the cylinder to expand. The total and permanent volumetric expansions of the cylinder are determined by measuring the amount of water displaced by the expansion of the cylinder when under pressure and after the pressure has been released. An external and internal visual inspection of the cylinder is also performed, along with a dead-ring test for steel cylinders. We are reputed practitioners of cylinder hydro testing, also known as a hydrostatic stretch test, which refers to testing all gas cylinders. However, due to specific reasons, we don’t test the disposable gas bottles and cylinders of acetylene, carbon dioxide, liquid hydrocarbons and welded gas cylinders regardless of cylinder MOC. We encourage regular hydro testing of all other cylinders to ensure that they are in proper working condition and can be used for future purposes. Hydrotesting is only performed under specific procedures and can’t monitor the equipment for leakage. Though hydrostatic testing is a non-destructive testing procedure, the equipment tends to rupture or fail should the inspection exceed a certain test pressure or if cylinder walls develop tiny cracks. We at Alchemie gases & Chemicals pvt Ltd. Offers hydrostatic testing of below specified cylinders which are manufactured as per the standards prescribed by CCOE, petroleum & Explosive safety organisation, ( Government of India) Co2 fire extinguisher, 1 lit to 68 lit
Why is cylinder hydro testing important?
According to the guidelines of The Petroleum and Explosives Safety Organisation (PESO), every gas manufacturing company must perform regular hydro-testing procedures on high-pressure seamless cylinders after every five years. They can undertake this examination at any time of the cylinder’s lifecycle, depending upon their existing condition. Toxic gas and CNG gas cylinders should be regularly hydro-tested every two years or at an interval specified by the PESO. A cylinder is hydraulically tested at the “test pressure”, which could be 1.5 or 1.66 times the normal working pressure. Of course, the amount depends upon the cylinder’s manufacturing standards and MOC. Regular hydro testing is performed to evaluate the cylinder material’s elasticity as it undergoes elastic expansion or stress during the gas filling process. The elasticity must be checked to see the material has returned to its original position within a specific tolerance limit. With repetition and time, its elasticity deteriorates, making it unsafe for further use.
How is hydro-testing performed ?
Hydrotesting refers to a pressure test where the worker fills the container with water, removes the air contained within the unit and pressurizes the system for up to 1.5 times the designed pressure limit of the unit. The worker retains the pressure for a certain amount of time to inspect the system visually for leakage. This is further enhanced by applying fluorescent dyes or tracers to the liquid to check for new leakages and cracks. Three hydrostatic testing methods are used to test small pressure cylinders and vessels:. Water jacket method - The worker fills the cylinder with water and loads it into a sealed chamber (the test jacket), also filled with water. Next, the vessel is pressurized inside the test jacket, which causes the vessel to expand and causes the water to force itself into the glass tube that measures the total expansion. Once recorded, the worker depressurizes the vessel, and the water flows back into the test jacket. If the vessel doesn’t return to its original size, the second size value is renamed permanent expansion. The worker determines the difference between permanent and total expansion, and the vessel is decommissioned if the value is higher. Proof pressure method- The worker causes internal pressure on the vessels to check for wall thinning, leakage or defects. Pneumatic testing involves the worker pressuring the vessel with nitrogen or air instead of water, which must be carefully performed as gaseous mediums can be compressed in large amounts compared to hydro testing. Cylinder hydro testing results are measured in terms of the Percentage Permanent Expansion and must fall within limits prescribed by the PESO. Hydro tests for pipelines are conducted out-of-service pipelines, natural gas or oil is turned off, and the line is cleaned before testing. Reach out to us at Alchemie Gases & Chemicals to meet your requirement.
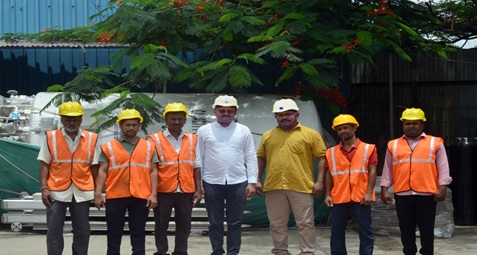
Training In Gas Handling
We provide a wide range of safety training workshops and courses to support the safety needs of your business and employees. Our training courses include safety in gas cylinder handling and best practices to be used at workplace.
This training will include following points:
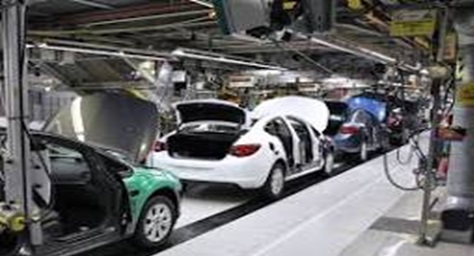
Industries
We are serving all industries such as Automotive Industry, Pharmaceuticals, Cement Industries, 4. Fertilizers, Food & Beverages, Hospitals, Instrumentation, Laser gas, Lighting Industries, Metal Manufacturing & Fabrication, Petrochemical & Refineries (Oil & Gas), Research / Laboratories
PURE GASES CGA SELECTION CHART FOR FITTINGS
It is recommended that the user thoroughly familiarize himself with the specific properties of these gases. The Compressed Gas Association (CGA) has selected and standardized the valve outlet to be used on each gas cylinder. These standards, contained in the document “CGA STANDARD V-1, Compressed Gas Cylinder Valve Outlet Connections” , have been adopted to prevent the inadvertent mixing of gases which could be reactive and to avoid other possible misuse hazards. The above chart may be used for guide purposes only. Consult your gas supplier to determine the actual CGA connection required when ordering a regulator.
CGA Fittings Required | Pure Gases |
---|---|
510/300 | Acetylene |
510/300 | Acetylene | 590/346/347/702 | Air |
240/660/705 | Ammonia | 580/680/677 | Argon |
350 | Arsine* | 320 | Carbon Dioxide |
350 | Carbon Monoxide | 660 | Chlorine |
510 | Cyclopropane | 350 | Deuterium |
350 | Ethane |
350 | Ethylene |
510 | Ethylene Oxide |
580/680/677 | Helium |
350/695/703 | Hydrogen |
330 | Hydrogen Chloride |
330 | Hydrogen Sulfide |
580 | Krypton |
350/695/703 | Methane |
510 | Methyl Chloride |
580/680/677 | Neon |
580/680/677 | Nitrogen |
326 | Nitrous Oxide |
540/577/701 | Oxygen* |
350 | Phosphine |
510 | Propane |
350 | Silane* |
668/660 | Sulfur Dioxide |
590 | Sulfur Hexaflouride |
580/680/677 | Xenon |
MIXED GASES CGA SELECTION CHART FOR FITTINGS
Since the combined characteristics of a mixture of gases often differ from the properties of the separate components, different CGA connections are often required. The CGA has selected and standardized the valve outlets to be used with mixed gases. These standards are described in CGA publication V-7 - “Standard Method for Determining Cylinder Valve Outlet Connections for Industrial Gas Mixtures”. Mixtures which use the same CGA connection as if the minor component were in its pure gas form have not been included for the sake of brevity. The proper fitting for these mix- tures can be determined by looking up the minor component on the chart for pure gases.
CGA Fittings Required | Mixed Gases | |
---|---|---|
Minor Component | Major Component | |
240/660/705 | Ammonia | Nitrogen |
350 | Butane | Nitrogen |
296 | Carbon Dioxide | Oxygen |
580 | Carbon Dioxide | Helium or Nitrogen |
580 | Carbon Dioxide and/or Nitrogen | Helium |
590 | Carbon Monoxide | Air |
330 | Chlorine | Nitrogen |
350 | Diborane | Argon, Helium, Hydrogen, Nitrogen |
580 | Freon-12 | Nitrogen |
296 | Helium | Oxygen |
350 | Hexane | Nitrogen |
350 | Isobutane | Nitrogen |
580 | Krypton | Argon |
590 | Methane | Air |
580 | Moisture | Argon, Helium or Nitrogen |
660 | Nitric Oxide | Nitrogen |
660 | Nitrogen Dioxide | Air or Nitrogen |
590 | Nitrous Oxide | Nitrogen |
590 | Oxygen | Nitrogen or Helium |
350 | Propane | Nitrogen or Helium |
590 | Propane | Air |
660 | Sulfur Dioxide | Air or Nitrogen |
590 | Sulfur Hexaflouride | Argon, Helium or Nitrogen |
350 | Sulfur Hexaflouride | Hydrogen |
1. Liquid- Argon
Liquid Argon is a colorless, odorless, tasteless and nontoxic gas. Argon belongs to the family of rare gases. Tasteless and extremely cold Argon forms no known chemical compounds. The gas is 1.38 times heavier than air and is slightly soluble in water.
Argon is present in the atmosphere at a concentration of 0.93%. Argon is recovered from air in an Air Separation Unit (ASU) where it is drawn off as a cryogenic liquid at about -303°F. Argon can then be distributed as a cryogenic liquid or as a gas in cylinders.Safety Informations
Argon is an inert gas that causes oxygen depletion leading to asphyxiation and death. The danger is exacerbated by the fact that argon’s density is greater than air. This allows it to flow downwards and collect in low lying areas far from the point of leakage. Argon is not consumed in any process and might, therefore, be present in high concentration in exhaust streams. Argon used in electric welding operations can fill the tanks and vessels being constructed and lead to asphyxiation hazards. In its liquid form argon represents a frostbite hazard.
Specifications (available) - PURITY :- > 99.9997%
2. Liquid-Oxygen
Oxygen is a colorless, odorless and tasteless gas that supports life and combustion. All elements, except rare gases, react with oxygen, over a wide range of temperatures, to form oxides. Oxygen is 1.1 times heavier than air and is slightly soluble in water.
Safety Informations
- Oxygen is not toxic at atmospheric pressures
- Oxygen deficient atmospheres cause asphyxiation and death
- Oxygen enrichment is just as dangerous and difficult to detect
- Clothing and flammable materials will burn violently if impregnated with oxygen.
- Oxygen reacts violently with oil and may spontaneously burn with an explosive force.
3. Liquid- Nitrogen
Nitrogen is colorless, odorless and tasteless. It is nonflammable, will not support combustion and is not life-supporting. The gas is slightly lighter than air and is only slightly soluble in water. When liquid nitrogen is vaporized and then heated it consumes a large amount of heat, making it an ideal coolant.
4. Liquid- Distribution Methods (AR/N2/O2)
Liquefied gases are transported in tank trucks with trailers and stored in cryogenic vessels. These tanks are available in various sizes, ranging from 3000 to 24,000 ltrs, to suit the customer’s requirement. The delivery system includes piping which carries gas from the inner vessel through the vacuum jacket to the outside, controlled by gauges and valves mounted outside of the ta Other relevant accessories such as evaporators and remote tank-level monitoring are also available as required. An uninterrupted supply of either liquid or gas is thus assured at all times. We install 1 KL cryogenic tanks in customer premises for bulk users on a contract basis, The 1 KL tanks are refilled by our fleet of liquid tankers as, and when required by the customer. This will give uninterrupted gas supply and is highly beneficial to the customer.
5. Dura-Cyl Low Pressure Liquid Cylinders
Dura-cyl low pressure liquid cylinders provide the longest holding time, lowest evaporation rate, highest gas-withdrawal rate and best life-cycle cost. Each 200 lts Dura can replace 20 compressed gas cylinders, and is a very good replacement for bulk cylinder users.
- Ideal for liquid nitrogen, oxygen and Argon.
- Stainless-steel vessel.
- Thicker, dent-resistant outer shell.
- Durable, inner-vessel support system
- Heavy duty foot ring and large diameter handling ring with four supports.
Product Highlights
6. Liquid Nitrogen Cans
We offer a wide range of Liquid Nitrogen Container,which finds its usage in artificial insemination programs, laboratories and small consumers of liquid nitrogen. Our sturdy, efficient, light weight and compact containers display amazing performance in terms of lower evaporation loss, longer holding time and adaptability to Indian road conditions. Features like double walled aluminum vessel, fiber glass neck tube and super insulation reduce heat losses to the lowest uniform levels. The capacity of Liquid Nitrogen Containers ranges from one liter to a maximum of 55 liters.


Specialty or High-purity Gases
What are specialty or high-purity gases?
We produce and supply specialty gases, which are extensively used in laboratory analysis and industrial applications. Specialty or high-purity gases (mixtures) are products that have met all the requirements of component purity and impurity content, are manufactured as per specific technology, and are used in tiny amounts for scientific, technological and analytical (metrological) purposes. Also, they satisfy most requirements related to diffusive resistance, hermiticity and reactivity. High-purity gases manufactured by top-notch companies include high-purity calibration gas mixtures, liquid gases, cylinder gases, mixtures for medical tools sterilisation and laser mixtures. We select a suitable specialty gas, proper gas packaging and delivery system, and optimise the process with our high-purity gas specialists to review the operations and deliver products manufactured and approved by qualified laboratory technicians who use advanced analytical technology to meet the customer specifications. High-purity gases include argon, air, carbon dioxide, helium, hydrogen, oxygen, nitrogen, hydrocarbons, rare gases, customised gas mixtures and EPA protocol gases.
Where are high-purity gases used?
We manufacture and package our high-quality gases by checking raw material quality with analytical methods such as atomic emission spectrometry, chromatography atomic absorption and more. We ecologically monitor the highly toxic and explosive substances in the atmosphere while maintaining an inert, protective and reducing atmosphere. They further aid in the production of UHP gases. Manufacturing companies also work with high-purity gases, which help research, laser technology, clinical diagnosis and chemical synthesis. High-purity gases are commonly used in analytical activities as they provide reliable and consistent results. They work with the lowest level of impurities available, and general applications consist of the calibration of research, material testing and instrument. High-purity nitrogen is popularly used in casting heat treatment, food packaging, secondary steel refining, lamp industries and optical fibres. High-purity hydrogen and helium are used in gas chromatographs, while high-purity argon is used as the carrier gas for microelectronics and gas chromatographs.
We offer a complete range of specialty high-purity gases!
As we have worked with gases for multiple decades, we know that each gas comes with a purpose. From argon to xenon, we offer all kinds of pure gases: noble gases (helium, krypton, neon, and xenon), air gases (argon, nitrogen, and oxygen), hydrogen, carbon dioxide, hydrocarbons, and carbon monoxide. We also have inorganic gases (ammonia, sulphur dioxide, and chlorine) and organic gases (acetylene, ethylene, ethane, propane, propylene, butane, hexane, and methane). Our products are manufactured and packaged while adhering to stringent product quality standards. We use advanced analytical equipment that complies with global regulations, is managed by qualified and experienced laboratory technicians, and carefully sourced raw materials. In addition, we have provided the proper training to our sales team, so that they understand your requirement, suggest the correct products and packaging to ensure industry specifications and customer expectations.
You can trust our products!
We manufacture our products with the utmost consideration for stringent quality standards, starting from the raw materials, production stages, and compliance with government regulations. Our company follows all quality guidelines as set by the highest authority of India and adhere to the control measurements and individual cylinder analysis, which determines the gas quality requirement. In addition, we use several applications, specifications, and instruments to measure gas purity and removing impurities. We have different grading systems to measure UHP gas purity. Our products are available across all shapes and sizes, right from bulk supply down to tiny cylinders. We understand that different companies have specific sets of requirements, which is why we’re happy to take customized orders. Our experts would be happy to select the right product, package, and deliver high-purity gases for your requirements. All you have to do is to book an appointment with us. So, check out our entire portfolio at Alchemie Gases & Chemicals to learn more about our ultra-pure gases, ready to be delivered at your service.
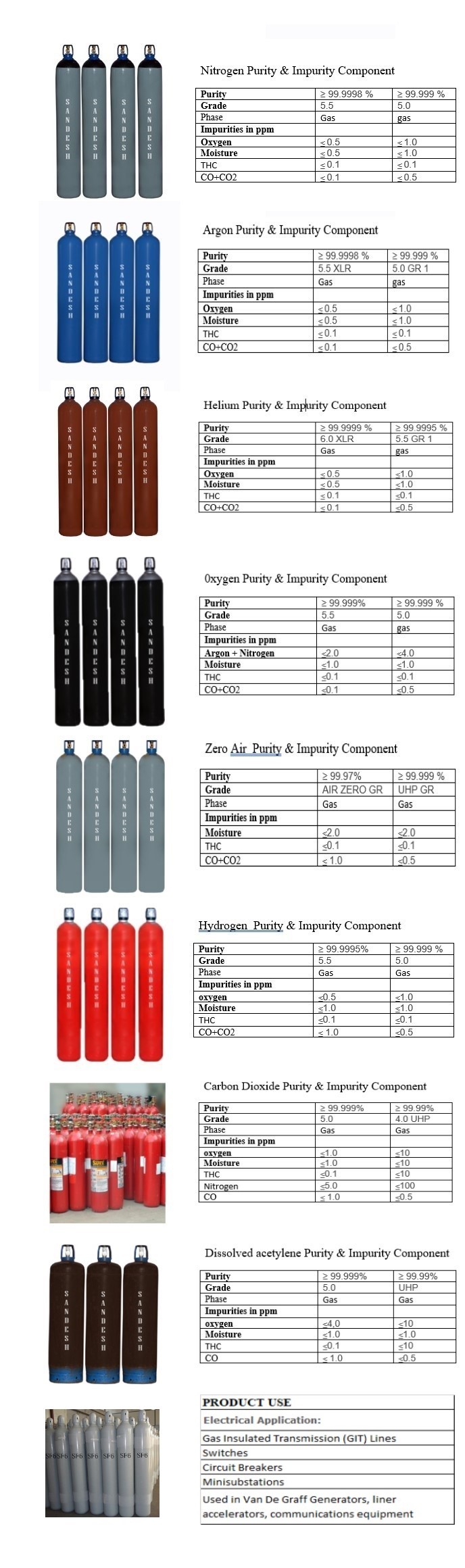
Gas Mixtures
1% Accuracy Gases |
Reactive Single Component |
Reactive Multigas Component |
Non-Reactive Multigas Component |
We handle over 100 different types of gases and liquid chemicals to produce 5000 varieties of Gas / Liquid mixtures to serve the ever increasing need of Industries and Institutions. The gas mixtures are made to any concentration within the permissible limits of Physics and Chemistry. This is non-explosive, non-reactive, stable mixture of gases in wide range of packaging. All Specialty Gases are custom-mixed and analyzed, and then properly labeled in facilities. We manufacture our calibration gas mixtures with state-of-the-art and advanced gravimetric scales, tools, and instruments. There are several cylinder sizes in place to fulfill your specific gas requirements, which can be viewed on the cylinder specification page and mixture component page. Our business always provides and markets high-quality specialty gases, and equipment by directly delivering them to the customers or distribution partners. We are constantly guided by our belief that only top-notch products are offered to the clients. We also emphasize that our impeccable customer service takes the stage to provide profitable growth in the competitive gas industry
STABILITY
This is the time period for which the concentration of the components does not change and remain stable within certification accuracy irrespective of cylinder pressure and temperature. The certificate contains information on minimum pressure and temperature range needed for use of the mixture before the concentration may deviate from certified accuracy.
QUALITY ASSURANCE & TRACEBILITY
In order to supply calibration gas mixtures in accordance with specifications agreed upon with our customers, UPG has an efficient quality assurance system. All stages of production process, from receipt of order to dispatch, are subjected to strict quality assurance requirements.
NIST Traceable Standards
Sandesh gases Pvt Ltd. offers several calibration gas standards for automotive industries to meet the accuracy level. Calibration of instruments is done by NABL accredited labs. Our production facility conforms to a strict set of quality-assurance measures and standard operating procedures. Our lab has been certified and documented to be compliant with ISO/ IEC 17025 requirements.
Ripening gas
Fruit ripening is a biological process in which ethylene gas is generated by the fruits which in turn also acts in causing further acceleration of the ripening process. Thus one can start and trigger the process of ripening of fruits by introducing ethylene in some form. It is also known that the ripening can be started by introducing acetylene; acetylene is generated by keeping small quantities of calcium carbide particles or dust. This carbide while coming into contact with moist atmospheric air causes generation of acetylene which in turn warms up the atmosphere as well as known to trigger the ripening in fruits. It is suspected that the ripening process is accelerated since acetylene imitates ethylene. Since the amount of carbide needed to ripen the immature fruit is more it makes the fruit become more tasteless and toxic. Also commercially available carbide is known to contain trace amount of arsenic and phosphorous in carbide that can make the healthy fruits poisonous. It is also known that the fruit ripening using calcium carbide is banned by Govt. of India. Ethylene also can be generated from ethanol and other ethylene derivatives. However ethanol is a restricted items as this can be used as and imbibed as an alcohol and thus possession of ethanol can lead to avoidable inquiries and harassment by many govt. and police authorities. Use of ethylene in pure form in small and safe quantities or as safe mixtures of ethylene and nitrogen are the recommended and best methods for ripening of fruits.
For Fruit Ripening
The quantity supplied in sealed cans is safe as long as the seals are not broken. The quantity in each can is adequate to ripen approx. 3 to 4 tonnes of bananas when mixed with air in a sealed chamber
Ethylene in Canister Can:
Why Ethylene? Ethylene is an agent in the fruit ripening process. Most of the fruits elute ethylene gas as they ripen and other is sensitive to it. The process of ripening is triggered and accelerated, if the atmosphere surrounding the raw fruit is injected with trace of ethylene gas. The process of fruit ripening with external ethylene injection does not affect the flavor and taste of the fruit. The concentration of ethylene that is required to be maintained in the atmosphere during the soaking period is decided by the size of the room/chamber and the type of fruit. One canister shall result in a concentration of approx. 100 ppm of ethylene in a room/chamber of size 3M*4M*3M, with a volume of 36cubic meter (36000litrs). How to use: Store the fruit in plastic crates/tray in a gas tight room or a chamber to avoid physical damage to the fruits. Reduce the room temperature to prescribe temperature for the fruit. (15 to 18 Deg. C for bananas). Break the seal of the canister valves and press the canister valve to release the gas into the room/chamber. Empty the canister completely. Care should be taken that the operator is not exposed to gas eluting from the canister. The room should be gas tight and shall have adequate air circulation facility to ensure that the concentration within the room is distrusted and uniform. After the prescribe time (for banana 24 hours). Open the doors of the room for 20minutes. Six hours for the next 24 hours to ventilate the room and remove CO2 from the room. Remove the fruit crates for strong and transport to next stage.
A Guide for Fruit Ripening:
Fruits are ripened with ethylene exposure at certain prescribed Temperature and Relative Humidity level of 90-95%. Following is broad guide for fruit ripening condition.
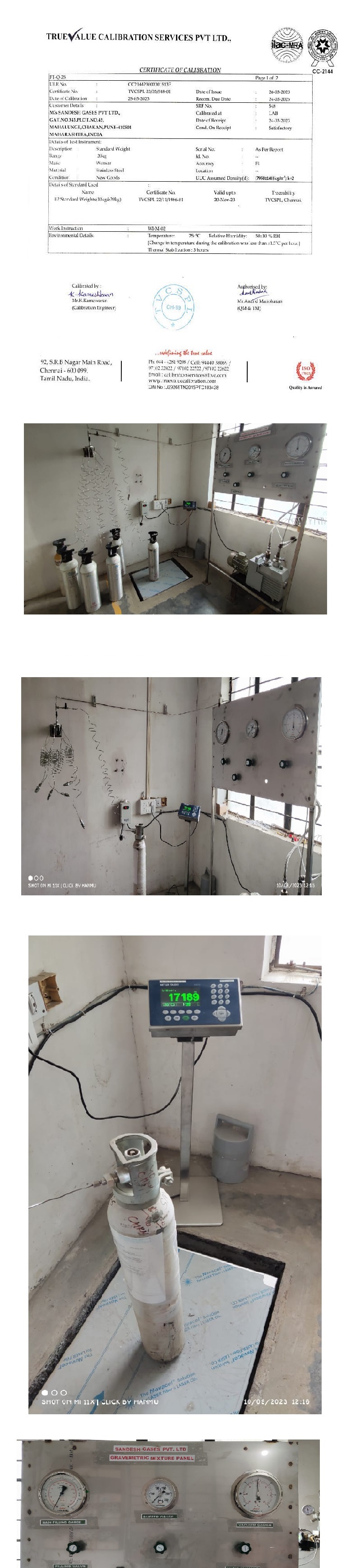
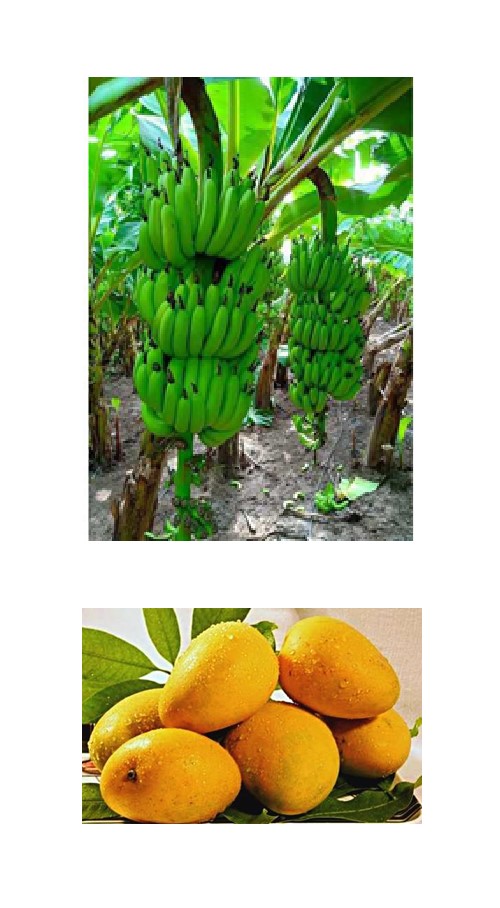
Parts Available for Specific Requirement of Customer
Specialty gases typically refer to calibration gases, zero gases, carrier gases, span gases, instrumentation gases and bump test gases. They may be either pure gases or gas mixtures containing components at concentrations extending from the per cent range down to part per billion and sometimes even part per trillion.
Gases | Purity% | Gases | Purity% |
---|---|---|---|
METHANE | ≥99.95% | CARBON DIOXIDE | ≥99.995% |
METHANE | ≥99.995% | CARBON MONIXIDE | ≥99.97% |
METHANE | ≥99.999% | CARBONYL SULPHIDE | ≥99.90% |
ETHANE | ≥99.95% | METHYL MERCAPTAN | ≥99.50% |
ETHYLENE | ≥99.995% | ETHYL MERCAPTAN | ≥97.00% |
PROPANE | ≥99.50% | ETHYL ACETYLENE | ≥98.00% |
PROPANE | ≥99.90% | VINYL ACETYLENE | ≥98.00% |
ISO-BUTANE | ≥99.50% | VINYL CHLORIDE | ≥99.97% |
ISO-BUTYLENE | ≥99.50% | HYDROGEN SULPHIDE | ≥99.50% |
I-BUTANE | ≥99.00% | XENON | ≥99.999% |
N-BUTANE | ≥99.50% | NEON | ≥99.999% |
1, 2 BUTADIENE | ≥98.00% | KRYPTON | ≥99.999% |
1, 2 BUTADIENE | ≥99.50% | SULFUR | ≥99.99% |
CIS-2 BUTENE | ≥99.00% | HCL | ≥99.995% |
TRANS 2 BUTENE | ≥99.00% | ARGON | ≥99.9999% |
PROPYLENE | ≥99.50% | NITROGEN | ≥99.9999% |
PROPYLENE | ≥99.90% | AIR (SYNTHETIC) | ≥99.90% |
PROPADIENE | ≥95.00% | HELIUM | ≥99.9999% |
CYCLOPROPANE | ≥99.00% | HYDROGEN | ≥99.9999% |
NITRIC OXIDE | ≥99.50% | OXYGEN | ≥99.999% |
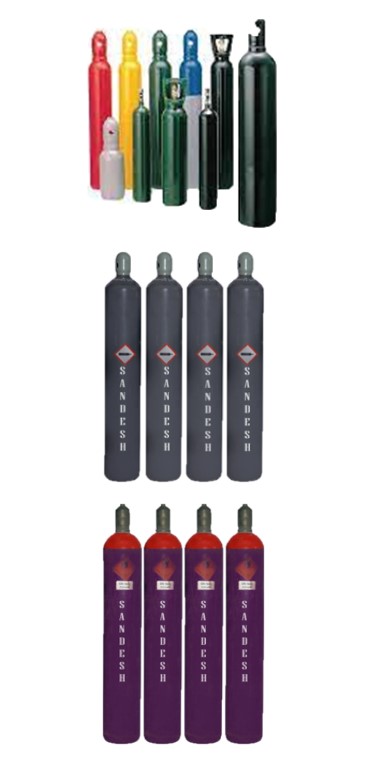
Gas Handiling
We also offers a complete range of Gas Handling Equipment that include Cylinders, Regulators (I & II stages, Brass & SS), Manifold Systems, gas cyls Pallets, Gauges, Flow meter, Cylinder Trolley, Valve & Valve Cap & Guard, Cylinder Quad, Aluminium Canister, S.S. Bottle and other safety products supported by a broad range of related services.
Single stage gas pressure regulator |
Flexible Hose |
Gas purification panel |
Gas cylinder trolly |
Cylinder Quads |
Cascades |
Pallets |
Banks |
- Knurled ON/OFF knob for easy grip with or without gloves
- Rotate knob for audible ON/OFF click
- No set screw on the knob, meaning the knob won’t strip out
- Wide diaphragm design for precise flow control even as the cylinder pressure changes
- Finer graduations for precise reading of cylinder contents
- Stainless steel gauge
- All wetted surfaces have proprietary passivated coating to ensure non-reaction with calibration gas
- Wide choice of outlets and inlets available
- Side outlet prevents tubing from kinking
How to choose the correct type of regulator for your purpose : Here we would like to explain to our customers about gas pressure regulators. In the process of regulator selection, the application needs to be defined with consideration given not only to the pressure requirements but also to the flow rate, gas/liquid composition, and temperature. Proper selection can help to avoid undesirable conditions such as droop and creep, improper pressure control, and contamination of gas streams. Once the appropriate type of regulator has been identified, based on the application, attention should be given to the materials of construction (MOC). The same regulator may be outfitted with different materials for critical components such as diaphragms and poppet seats, to ensure the safe and proper functioning of the regulator over time. The high-pressure gas regulators are of two types i.e. Single Stage & Two Stages. Single Stage and Double stage Regulator : There are 2 basic Gas Pressure Regulators are available in the market. We request our customers to consider choosing between a single and double-stage industrial gas regulator. It depends on the variation in the inlet pressure supply. The manner in which a regulator adjusts to variations in the high-pressure supply is known as the supply pressure effect (SPE). In short, Single pressure regulators are suitable for most applications where the inlet pressure is relatively constant, whereas the high-pressure supply is subject to large variations, a two-stage regulator with a low SPE will provide the most stable, low-pressure delivery. Piston type Regulator : Piston type Gas Pressure regulators are generally used in applications with outlet pressures higher than 35 bar, although they may also be suitable for lower pressures. The Series 100 regulators from PortaGas are designed to maintain constant flow rates so you get real accurate monitor calibrations even as the cylinder pressure drops.
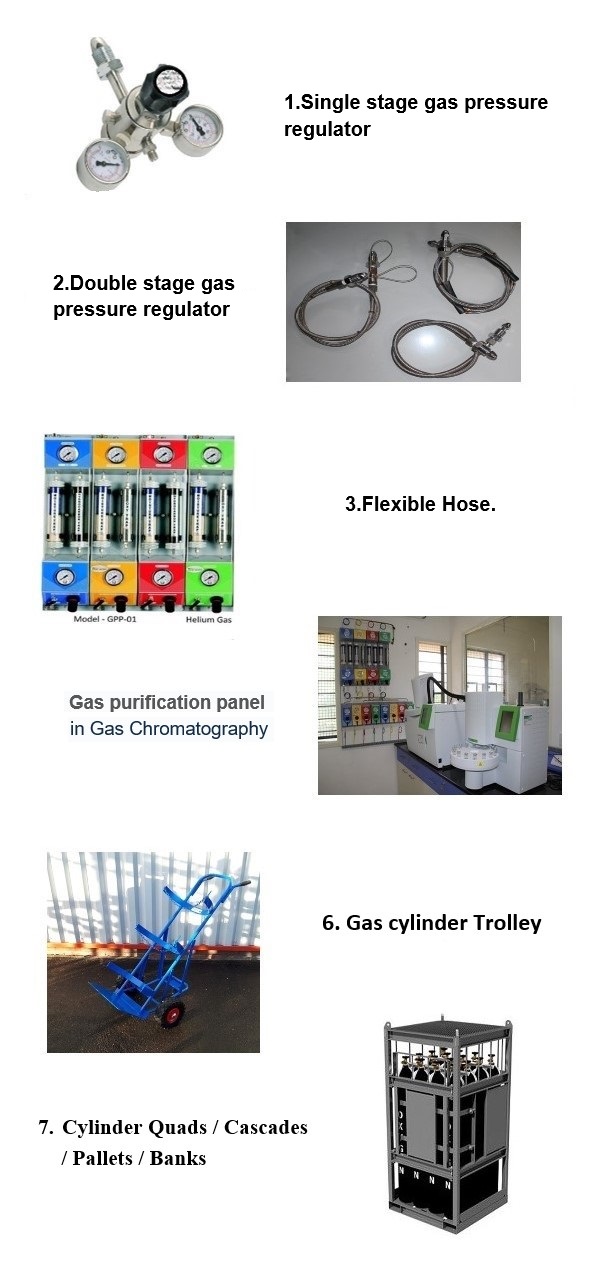
Gas Mixing Panels
BSL Gas Technologies Ltd make a range of standard panels suitable for industrial applications and each of these panels are pre-set to suit the customers’ specific needs prior to despatch. The capacities shown below are approximate, and are dependent on inlet pressure, outlet pressure and gas type. 25m³/h Mixing Panel - BSL Basic Stock Code Number FW1 50m³/h Mixing Panel - BSL Basic Stock Code Number FW2 100m³/h Mixing Panel - BSL Basic Stock Code Number FW3.
System Description The mixing panel is designed to mix two or three gases by means of pre-set gas mixers and supply the resulting mixed gas into a pipeline distribution system. The panel is fitted with 1, 2 or 3 of BSL Gas Technologies patented mixing valves, depending on the capacity. The gas mixers work on a pressure balance principle with an interlock so that both inlet gases must be present for there to be a mixed gas output. Each mixer has been configured internally to suit the particular gas application and mix required from the system and should not be tampered with and or adjusted by non-qualified personnel. Gas mixing valve outlets are manifolded together where necessary to provide the correct gas flow for the panel design.
Inlet Gas Supply As standard, pressure regulators and pressure relief valves are not provided for the gas inlets. It is the responsibility of the customer to provide gases at the correct pressure and to fit pressure relief valves (if required) to ensure that the design pressure is never exceeded. It is important for the correct operation of the equipment that inlet gas supply pressures are at or below the limits specified on the panel data label. However, the pressures of the inlet gases must also be within a specific range relative to each other - an additional label will be attached to the lower right hand side of the panel back plate giving details of the required relationship between all the inlet gases. Mixing panel performance and gas mixture control will be impaired if the instructions on this label are not followed. The gases supplied to the panel must be clean, dry and fully vaporised. Liquid gas may damage the system or cause injury. Gas supply lines to panel must be clean and free of debris. Unless their omission is specially requested by the customer, the mixing panel inlets and individual gas mixing valves are fitted with 300 mesh filters to protect them from dirt ingress caused by making pipe connections to the panel. They are not designed to filter the gas supply itself. If there is any doubt about the cleanliness of the gas then a filter of 5 m or better should be installed in the gas supply line close to the mixing panel. In the case of CO2 it is sometimes necessary to fit a 0.01 m coalescing filter and an activated carbon filter to ensure that any impurities in the gas or plasticizer from hose linings is removed. Liquid CO2 is a powerful solvent and may carry dissolved oil or extract plasticizers from flexible hose linings. Contamination of this sort will affect the gas mix. If Oxygen is used then all gas supplies, upstream and downstream pipework must be of suitable construction and cleaned to Oxygen standards. Mixed Gas Outlet A pressure regulator is optionally fitted to the mixed gas outlet. This is adjustable 0 to 13.8 bar. Please note that panel will only produce the rated capacity with the gases and inlet and outlet pressures specified on the customer’s original order. Pressure relief valves are not fitted in the mixing panel. In the event of component failure the mixed gas pressure could equal the gas supply pressure. If equipment downstream of the mixing panel cannot withstand this pressure then customer must install suitable pressure relief valves.
Panels For Special Applications BSL Gas Technologies Ltd can also offer versions of the FW series panels for special purposes, please contact us with your requirements. One example of this is the FW2 type panel with user adjustable mixture setting. FW1, FW2 and FW3 Panels With User Adjustable Mixture Setting These panel types follow the same basic layout as the standard FW series, but use modified mixing valves that incorporate an end-user accessible adjustment mechanism. To change the gas mixture, insert the key provided in the hole as shown, turn clockwise to increase mix, and counter- clockwise to decrease. The mixture setting is indicated on the scale. BSL Gas Technologies recommend that customers use a gas analyser at the point of use. Replacement keys are available as spare parts from BSL Gas Technologies Ltd.
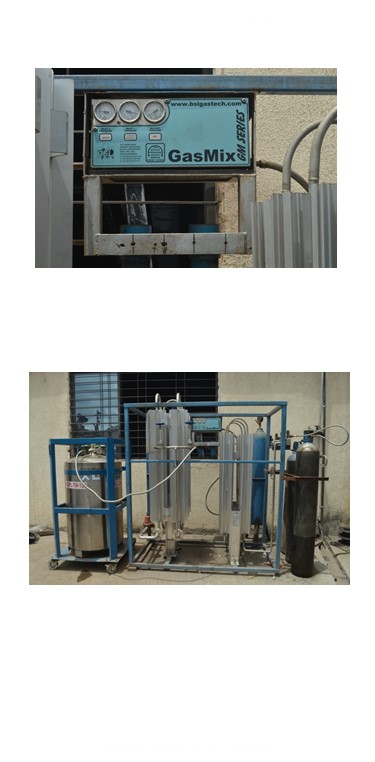
UHP Oxygen 5N,5.5N
We have installed Oxygen Plant to produce & certify 99.9995% pure Oxygen. SGPL is the only manufacturer in India to produce Oxygen gas up to 5.5 grade purity.
Grade |
≥ 99.999% |
≥ 99.999% |
5.5 |
5.0 |
|
UHP Oxygen |
√ (Available) |
√ (Available) |
UHP - OXYGEN 5.0 & 5.5 Grade –Purity and Impurity Component
Purtiy |
≥ 99.999% |
≥ 99.999% |
Grade |
5.5 |
5.0 |
Phase |
Gas |
Gas |
Impurities in PPM |
||
Argon + Nitrogen |
≤2.0 |
≤4.0 |
Moisture |
≤1.0 |
≤1.0 |
THC |
≤0.1 |
≤0.1 |
CO+CO2 |
≤0.1 |
≤0.5 |
Oxygen Ultra Pure
We are having speciality gases range includes a number of UHP (ultra-high purity) oxygen products with specifications intended to deliver peace of mind whatever your application. Whether it is chemical analysis or process control, our experts are on hand to help you select the right gas for your requirements. The range includes gas with unrivalled specifications of critical impurities and a comprehensive range of package options.
Benefits of Oxygen Ultra-Pure 5.0 & 5.5 Grade
For elemental analysis techniques the level of Nitrogen impurity in the reference and oxidant gases is usually critical because it is commonly the Nitrogen content of the sample which requires accurate detection and measurement. A high level of Nitrogen in these gases can severely affect the accuracy of the analyzer. Therefore, using Oxygen Ultra pure 5.0 & 5.5 Grade for this application which has < 1 part per million of this critical impurity can dramatically improve analyser sensitivity.
Featured Applications
- Aeration for Waste Water
- Annealing
- Artificial Insemination
- Balloon Inflation
- Beverage Dispense
- Blood and Cell Storage
- Brazing
- Campylobacter Intervention
- Cryogenic Chilling for Food
- Cutting
- Flame Ionization Detector(GC-FID)
- Food Freezing
- Gas Detection
- Hardening Crust Freezing
- Inductively Coupled Plasma ICP
- Laboratory Analysis
- Laser
- Pharmaceutical Gases and Cryogenic Storage
- Modified Atmosphere Packaging (MAP)
- pH Control for Swimming Pools
- Sintering
- Thermal Spray
- Welding
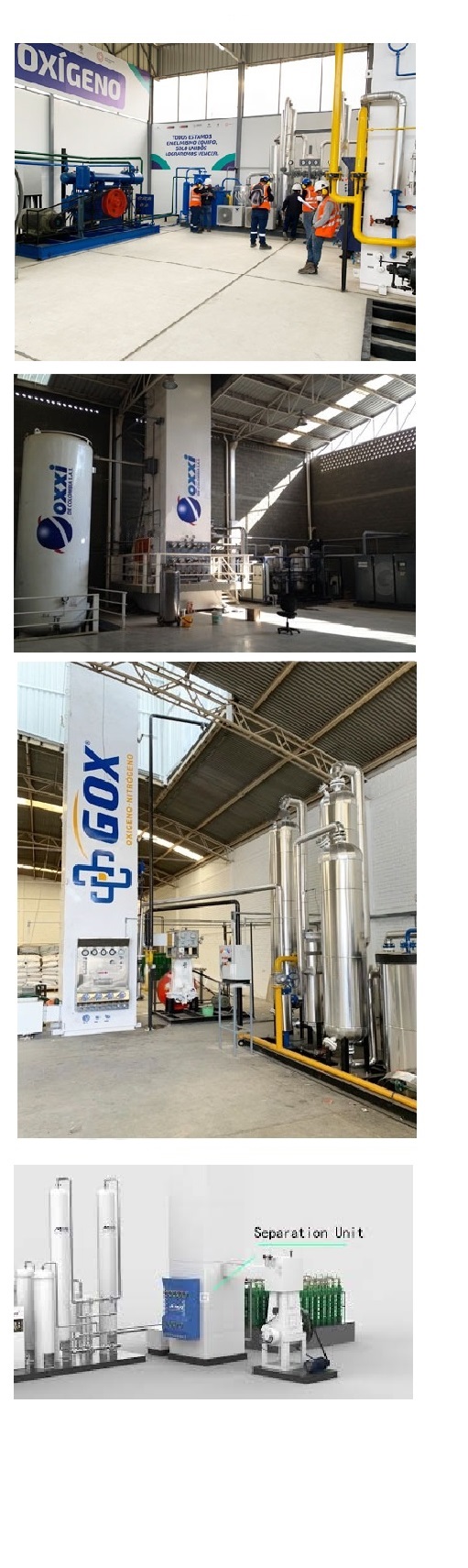
Upcoming plants Hydrogen Filling Plant
Hydrogen uhp grades manufacturing plant at SEZ Khed city Pune for quality of upto 6 N quality Hydrogen gas required in Diamond cutting Industries.
